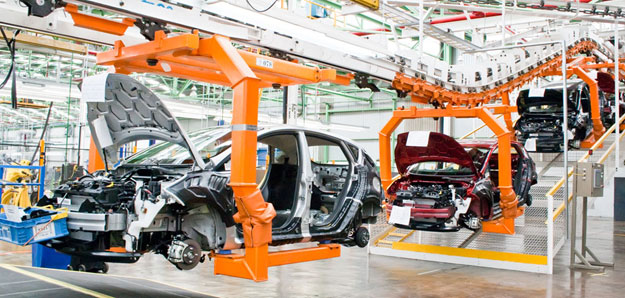
La planta de Ford en Cuautitlán recibió grandes cambios desde que fue aceptada la producción del Fiesta 2011 aquí para toda América. La inversión que recibió fue de mil millones de dólares, transformándola por completo.
Cuando se producía la F150 y demás versiones de la serie F de camiones Ford, existían únicamente 18 robots en toda la planta. Hoy en día hay 14 únicamente para pintura dando un total de 280.
Antes tampoco se contaba con área de estampado pero gracias a la enorme inversión, ahora cuenta con una de las dos estampadoras más modernas y avanzadas del mundo.
Las placas metálicas entran por un lado de la prensa. Una vez adentro se le aplica una presión que puede variar desde las 700 hasta las 2,500 toneladas dependiendo de la pieza que se este fabricando en el momento.
La máquina completamente automatizada, puede fabricar hasta dos piezas diferentes a la vez, además de contar con una capacidad de 13 a 16 piezas por minuto.
Una vez estampadas las diferentes piezas que conforman al Fiesta, se llevan a un área de almacenamiento donde se organizan para que los montacargas las puedan ubicar rápidamente y llevar al área de trabajo donde se necesitan.
Posteriormente, son llevadas a las diferentes celdas que se encargan del armado y soldado de la carrocería formando algunas veces partes pequeñas como salpicaduras, paredes de fuego, etc. que luego tienen que ser unidas para formar la carrocería completa.
Una vez listo, el “cascarón” es transportado a la planta de pintura mediante la línea de producción. Ahí es tratada con un sistema llamado TriWet que aplica la base, el fijador y la pintura en un solo paso para ahorrar energía y espacio.
Las carrocerías pintadas viajan de regreso a la línea de ensamble donde se separan las puertas para “vestirse” independientemente. Aquí se le instalan desde los componentes eléctricos, hasta tablero e inclusive los asientos.
Por otra parte, el motor es acoplado a la transmisión -ya sea automática o manual dependiendo de cada auto, a la suspensión y frenos para que quede todo en un mismo sitio y pueda ser insertado desde la parte de abajo al auto más adelante en la línea de producción.
Las llantas son lo último en agregarse y una vez hecho esto, se llenan todos los depósitos con los líquidos correspondientes como el anticongelante, aceite, frenos, etc. para pasar al área de pruebas.
Aquí, cada unidad tiene que pasar por una serie de pruebas para comprobar que la calidad del producto sea la ideal. Una de estas pruebas es la del viento a gran velocidad, otra la de lluvia en la que se buscan fugas que puedan entrar a la cabina y finalmente la de las luces en la que son alineadas perfectamente para iluminar la mayor área del camino enfrente del auto.
Al final de la línea de producción se encuentra el área de control de calidad en la que se examina detalladamente para encontrar imperfecciones en la carrocería, pintura, interior y por supuesto en el ensamble. Las unidades que no tengan problema alguno, están listas para ser guardadas en los patios y transportadas a su destino final y las que lo tengan, se tratará de corregir.
La producción de la planta es de 32 autos por hora durante dos turnos (por ahora pues se incrementará cuando se comience la producción para América del sur). Pero cuando esté a toda su capacidad, producirá hasta 451 autos diariamente.
Ahora la planta es una de las más avanzadas en el mundo pero también una de las más responsables con el medio ambiente pues cuentan con tratamiento de aguas residuales propio, chimeneas de pintura de las que no se emiten gases contaminantes y paros de energía cuando no es necesaria para consumir menos.
Actualmente cuenta con 1,600 empleados de los cuales un 15% son mujeres, algo nuevo para esta planta, pero se espera que aumenten aún más con el paso del tiempo.